一、模具粗加工的策略:
模具加工作为机械加工制造的典型,其制造水平的高低反映着一个国家的综合技术实力。各种类型的模具与注射模、压缩模、冲压模、级进模、压铸模等成型工艺技术的应用,都直接取决于模具制造精度、效率。模具常用铣削加工的策略是粗加工、办精加工、精加工、抛光及表面强化等的。下面对模具数控加工中常用的策略进行简单说明。
(1)基于毛坯的加工
采用基于毛坯的加工策略包含基于原始毛坯的等高分层加工和基于中间工序的残留毛坯加工两种方式,其数控加工金属切削的原理相同。目的都是实现刀具在加工过程中的余量均匀,刀具每次加工时所承受的切削力、切削深度、切削宽度相当,从而保持加工的平稳性,提高加工的效率。采用基于毛坯的刀具轨迹策略,对于提高模具的加工效率、提高刀具的使用寿命、保持机床精度、提高产品质量的有效途径。现有市面的CAM软件,UGNX和Cimatron、PowerMill等都提供了较好的基于毛坯加工编程的策略。
(2)型面比较复杂的加工
模具型腔和型芯的加工,其特征一般表现在型面比较复杂,大部分都是空间的三维曲面,因此曲面的铣削加工时,曲面的光顺性、表面光洁度等精度要求直接影响着产品的成型质量。常用的数控加工中心,多为三轴联动的数控机床。在模具铣削时,最常见的刀具轨迹策略是采用X、Z或Y、Z两轴联动,通过等歩距或变歩距行切的方式进行加工。这种方式对于模具的粗加工和精度要求不高的模具精加工(后续采用抛光工序)是可行的,但是对于模具的半精加工和精加工,这种方式不太理想,如果采用45度行切实现X、Y、Z三轴联动加工的策略,对于提高模具的半精加工和精加工的表面质量、光洁度有着非常明显的改善作用,这也是现代模具数控加工中心精加工的一种典型策略。
(3)深腔加工时的策略(钻削的影响优势与劣势)
对于大深度的模具型腔加工,如何提高粗加工的效率一直是机械加工的一个难题。典型常用的加工策略有钻削排量、钻铣排量、挖槽等高分层加工等几种方式。其中钻削排量的效率高,但是,钻削排量时,孔与孔之间形成的尖锐区是后续加工的难点,这些尖锐区无论采用铣削还是其它的方式,对于后续的精加工不利,尤其是锯齿状的侧面轮廓铣削时,由于余量非常不均匀,对刀具和机床冲击较大,严重影响了后续加工的顺利进行。相对单纯的钻削排量,采用钻铣刀进行钻铣排量时可有效避免钻削排量的缺点,但是由于钻铣刀的底刃相对于钻头的底刃来说,轴向的下刀及加工效率相对钻削排量要低得多,采用钻削排量+钻铣排量结合的方式是一种比较好的方式,主要余量部分采用钻削排量,尖锐区采用钻铣排量的方式。
等高分层的加工策略是比较稳妥的一种方式,但是对于铣刀的加工参数和刀具成本的控制策略相对比较复杂,尤其是中小型模具加工时,其附加值不高,刀具的成本在模具的粗加工时是企业必须考虑的一个重点要素,因此,必须在切削工艺参数和刀具的选择上作出合理科学的决策,如采用钻铣排量+等高分层切削也是一个比较好的选择。
(4)不同材料的加工
不同成型工艺方式的模具,其所采用的模具材料各不相同,市面上模具型腔型芯材料以黑色金属为主,占90%的比例,铝合金、锌和金、不锈钢材料的模具比例相对较小。黑色金属材料分两种典型的类型,经过调质后的中等硬度、综合性能比较高的的热处理状态和高硬度淬火的热处理状态。对于调质状态的模具加工,其加工性能相对较好,对刀具和机床的要求也相对较低。对高硬度淬火状态的黑色金属模具材料进行切削时,选择合适的刀具、合适的机床、合适的刀具轨迹策略、合适的工艺流程方案、合适的冷却方式、创造有利的排屑方式等等对于提高模具粗加工的效率是非常有意义的。而对于粘性材料如铝合金、不锈钢的加工,主要从刀具的选型、冷却润滑效果、切削工艺参数上进行合理的搭配即可,其难度相对于高硬度淬火状态的模具加工要小得多。
(5)变速切削策略(恒功率、扭矩、OMAT功能)
高速切削作为现代数控加工的趋势,其应用场合越来越广。但是对于一般的中小型企业,尤其是小型企业由于其使用成本高,,采用高速切削的策略应用不是很普遍,传统的数控加工策略模式所占的比重还是主流,因此如何有效的提高传统数控机床的铣削加工效率还是非常具有现实意义的。
传统数控机床进行铣削时,采用恒功率、恒扭矩的方式进行模具的粗加工策略是非常重要的,既可以有效的提高加工效率、保证产品质量的同时,可有效的降低刀具成本、保持机床的精度和寿命。在数控编程方面,Cimatron和UGNX均提供了较好的变速切削的策略,即针对不同的切削深度和宽度,使切削加工时的主轴转速、进给速度进行相应的调整来实现,而Vericut软件也可以通过程序优化的方式来保证加工的平稳性。使用好这些软件的前提是必须有一定的加工经验和较为丰富的数控编程经验,其对人的依赖性较大。
而采用硬件的方式,如通过数控机床的主轴监控或使用OMAT优化控制器来监测主轴的运转状况,通过有效的自适应控制方法来优化铣削加工时的转速S和进给速度F是非常有意义的,且OMAT是基于人工神经模糊控制策略的,因此其经验的积累可以不断的在加工过程中得到优化,使用自适应控制策略的时间越长,模具粗加工的效率越高、刀具的成本越来越低。
二、铣削刀具、刀柄、加工参数的合理搭配
1、主轴刀柄的选择
对于模具型面的粗加工来说,由于铣削时的切削力、扭矩比较大,因此加工时对主轴刀柄的刚性、主轴电机的扭矩和功率、伺服电机的进给推力有一定的要求。因此在粗加工阶段,尽量选择主轴电机功率大、刀柄刚性高的数控机床上来加工,如采用BT50的刀柄主轴或HSK100A的高速电主轴机床来加工。
2、刀具的选择
一般数控机床加工模具时,如果考虑刀具的成本,采用焊接硬质合金刀具来进行模具的粗加工时是可行的,但如何采用合理的切削参数,对于提高刀具的寿命是非常有意义的。对于模具的粗加工,采用等高分层的高速加工策略,采用镶齿刀片的刀具或整体硬质合金刀具来进行加工也是非常有效的一种途径。
3、不同切削刀具对应的切削深度、宽度、转速和进给速度的搭配
无论是采用传统的数控加工,还是高速切削的方式进行模具的粗加工,如下的几条原则都是非常有意义的。
(1)对称和非对称切削的应用:对刀具而言,采用非对称切削的方式,刀具在切削加工过程中,所承受的切削力小,主轴的扭矩也小。刀具在加工过程中,尤其是螺旋立铣刀,加工过程中一定要避免铣刀双侧受力。这样切削比较平稳,切削力小,切屑容易排出,对刀具的伤害比较小。铣刀铣削时,如果铣刀双侧受力时(满齿宽切削),由于切削力比较大、机床的振动、切屑的影响、主轴的跳动等对刀具、机床的要求较高,刀具磨损较快。原则上,要避免满齿宽切削,采用45~80%的铣削宽度是可行的。
(2)深度优先和宽度优先的选择:对于普通数控机床采用焊接硬质合金的螺旋立铣刀进行模具型腔型芯的加工时,在铣削深度和铣削宽度的选择上,满足相等金属切屑去除率的前提下,优先采用较深的铣削深度,采用相对较小的切削宽度是比较合理的。这是由于螺旋立铣刀在加工时,刀具的磨损集中在切削的部位,如果采用小深度、大宽度的方式,对刀具的寿命影响较大。采用大深度、相对窄的宽度进行铣削时,相同的刀具,其刀具耐用度较高。如采用20mm直径的铣刀进行粗加工时,采用切削深度10mm、切削宽度为8mm比采用切削深度5mm、切削宽度为12mm的加工参数相比,前者的刀具耐用度提高一倍,加工效率相对高20%左右,同时可以有效的降低刀具的成本。
对于高速切削机床的模具粗加工时,由于多采用镶齿的刀片进行型腔的加工,采用宽度优先、相对较小的深度来加工是比较合理的。这是由于高速机床加工时,要避免切削力过大对电主轴的损伤,另一方面,由于高速切削时要求采用较小的切削深度,可以有效的减小刀具的振动的同时来保证加工时的一致稳定性,减少对刀具和主轴的冲击。
(3)每齿切削量:无论是传统的数控铣削还是高速切削,主轴的转速、进给速度之间的关系,要结合被加工模具材料的特点来考虑。对金属切削而言,不同的工件材料,由于其材料的结构及机械性能的不同,材料的加工性能不同。如对于铝合金而言,要选择比较锋利的刀具如高速钢或硬质合金,粗加工时,每齿切削量在0.08mm~0.15mm之间是比较合理的。这是由于铝合金材料,其强度低、熔点低,在切削加工过程中,由于材料比较软,很容易粘刀。如果刀具不锋利,每齿切削量比较小时,刀具与工件之间是在摩擦,而不是在切削。
对于钢件模具型腔型芯的加工,刀具要选择强度比较高的硬质合金、立方氮化硼材料比较好,每齿的切削量控制在0.03~0.10mm之间是合理科学的。如果每齿切削量过小,刀具与工件发生摩擦,不是在切削;如果每齿切削量过大时,切削力大,刀具的磨损严重。如果采用整体硬质合金刀具或陶瓷刀具进行加工,在切削的稳定性控制方面要保证好,由于陶瓷材料和硬质合金抗冲击性比较差,很容易崩刃,因此尽可能避免加工过程中的振动和冲击。
三、模具数控铣削加工编程
如表1所示的某砖瓦橡皮模具成型时所用的瓦皮垫。现对该瓦皮垫成型的步骤进行简单介绍,重点说明如何通过对该产品进行逆向工程、模具设计、模具数控加工的基本流程进行了简要介绍。该产品逆向设计所用的软件平台为Imageware、采用UGNX进行模具设计,最后采用UGNX和Mastercam分别进行数控铣削加工编程。
(1)瓦皮产品与模具型面设计
如图1-图4所示,首先利用Atos扫描仪或FARO柔性关机臂坐标测量机等扫描设备对瓦皮产品进行三维点云扫描后,将点云导入逆向工程软件Imageware平台下,进行点云的处理,包括点云过滤、曲率分析、生成三维空间曲线后,利用Imageware中的逆向曲面造型功能完成产品的主要型面的反求造型设计。将逆向工程后期的产品曲面模型导入UGNX平台,利用UGNX软件强大的三维模具专家设计系统功能,快速高效的完成瓦皮凸模型面和凹模型面的详细设计。
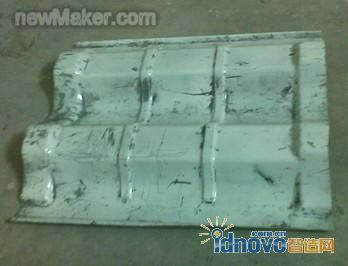
图1 产品三维点云扫描
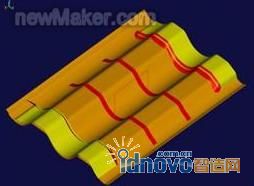
图2 Imageware平台下产品三维逆向造型

图3 UG NX平台下瓦皮凸模型面详细设计
(2)基于Mastercam的模具型面铣削编程
如图5-图10所示,在Mastercam环境下,对于该瓦皮模具型面铣削加工编程,常用的型腔粗加工排量方式有挖槽加工、浅平面铣削等方式,其中浅平面铣削加工是对挖槽加工的补充。半精加工有等高轮廓和曲面平行铣削两种方式,从图7和图8的轨迹可以看出,等高轮廓加工方式存在余量不均匀且不利于装夹的特点,因此对于该类型型腔半精加工采用曲面平行铣削方式比较好。对于精加工方式,采用平行铣削和平行换向铣削两种方式均可,但是鉴于模具型腔的表面光洁度要求,采用图10的轨迹方式进行加工,对于后续的抛光工序顺利进行比图9的轨迹方式要好。
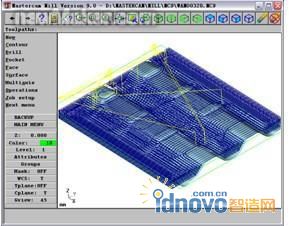
图5 挖槽粗加工排量
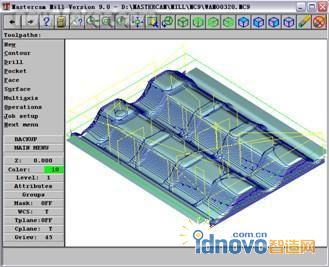
图7 等高轮廓半精加工
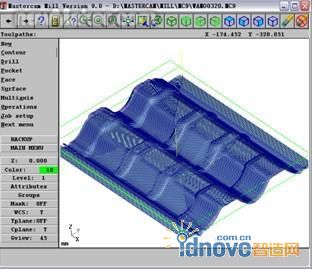
图9平行铣削精加工
(3)UGNX基于毛坯和残留的编程优势
如图11-图14所示,在UGNX环境下,对该模具型面进行数控铣削加工编程的流程依次为等高粗加工、残留加工、曲面流线半精加工和精加工。从中可以看出,由于提供了表面残余铣削加工的编程功能,对于提高编程的效率和加工效率是极其有利的。因此实际加工编程时采用了UGNX的编程功能和加工策略取得了较好的效果,其加工效率较传统的模具粗加工的效率提高了50%以上;图15是加工现场的效果图。
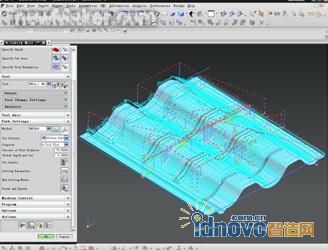
图11 等高粗加工轨迹
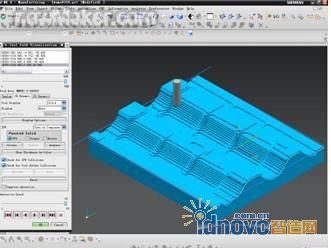
图13 型面刀具轨迹加工仿真
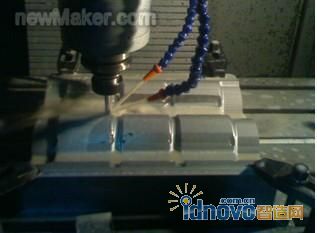
图15 加工现场
采用相同的策略,如图17和图18所示对某冲孔落料成型模具的凸模和压边圈进行数控铣削加工编程时,采用基于毛坯的方式铣削加工编程的策略。在测量毛坯实物的特征尺寸基础上,在UGNX环境下将毛坯设计完成后,首先采用立铣刀进行基于毛坯的等高分层加工的方式,然后利用球头铣刀进行半精加工和精加工,其加工效率比采用单纯的球头铣刀进行粗精加工的方式提高一倍以上。
采用立铣刀进行加工时,关键是要对毛坯进行测量,将毛坯的实际尺寸作为编程的毛坯模型,然后利用UGNX的基于毛坯的等高分层的策略进行刀具轨迹的编制和程序的输出。采用基于毛坯的刀具轨迹编制策略的优势在于可以有效的减少空刀,同时利用等高分层的策略结合毛坯识别的功能,可以保持刀具切削时轨迹的平稳性、流畅性和高效性。这种方式对于优化刀具轨迹、降低刀具的成本、提高模具的粗加工效率是非常有效的一种途径,对于模具企业的生产效率和成本是非常有意义的。
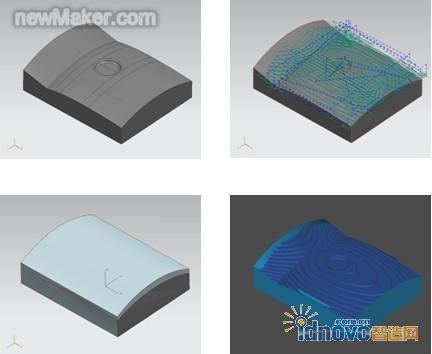
图17、凸模的毛坯及其粗精加工刀具轨迹
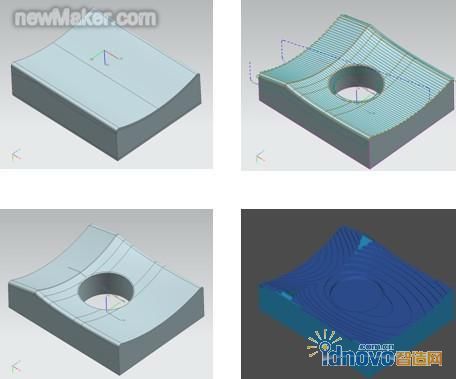
图18、压边圈的毛坯及其粗精加工刀具轨迹
四、小结
本文针对模具型面粗加工时,从数控机床主轴刀柄的选用、刀具的选型、切削参数的组合、刀具轨迹的编程策略等方面进行了讲解,围绕提高模具型面铣削粗加工时效率的途径进行了实例介绍,希望对读者有所参考借鉴作用。
参考文献
【1】高速切削技术及应用、机械工业出版社、张伯霖、2003
【2】金属切削原理、机械工业出版社、陈日曜、1995
【3】材料科学基础、机械工业出版社、石德珂、2002